about us
Automated Time Motion Study:
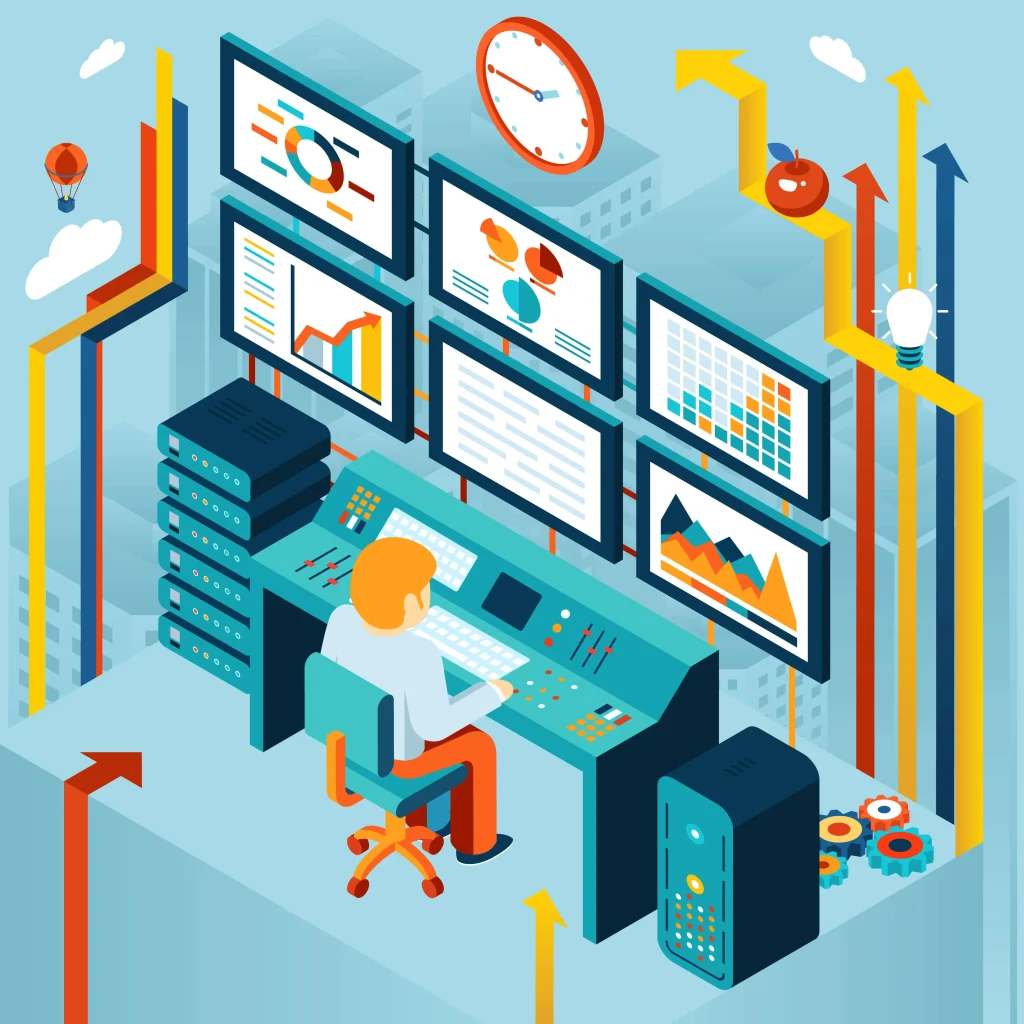
Monitoring Shell activities and detecting the activity time. Give a graphical dashboard for displaying the activities live with ML model detection. based on SOP times, calculate delay in each activity and generate report of the delays with defined reasons.
A steel melting shop has many activities, which include the different activities in the setup and the arching and blowing, tapping, End Brick Removal, HM launder pouring and positioning, and others. It starts with the hot metal from the blast furnace and ends after the first heat is completed with the tapping process. The existing condition before the use of computer vision-based machine learning for detecting the delays and reducing the setup time in the SMS, there was no other way to identify the specific cause of the delay. Also, it is not possible for someone to stand there while the process occurs and point out what is the delay is. We need a monitoring system. Through automatic monitoring we can look at a particular object, which might be a person or a tool for a particular process, and if a particular process is leading to a delay or not. In short, there was no old structure that could help in monitoring the activities and tell the delays. Delay can be very detrimental to any production facility as it slows down the production process, takes more time than needed, and so, the efficiency of the production goes down as a result. So, capturing the specific cause of delay might help in better work at each step of the process and would lead to better efficiency and save time.
There are four cameras (Front, side, EBT, tapping) per shell and there are four shells. End Brick Jam happens in the tapping camera while in EBT panel camera, mass filling and levelling is done. Tapping is the last activity of the heat and the first activity of next heat is EBT Jam Removal. There is a setup process that happens and then heating the metal (Arcing -pass the electricity or Blowing- blowing the oxygen) happens for an hour. SMS-starts when the hot metal comes from the blast furnace to the SMS and ends at tapping. Heat means the preparing of hot material. During the process, there are many Parallel and sequential activities. Now we will see each activity with details such as the start and end of the activity, the SOP time, the object for every activity and any additional information.
• Time motion study of the activities for SOP calculation for the activities.
• Using video feed from cameras the model was trained the track
different activities.
• Using these activities the process were monitoring for their times.
• The processed feed was used for live view to the clients.
Delay Time Tracking and Reasoning:
Achieved:
• Per Heat saving of 1min has been achieved.
• Increased number of heats pre day by 1-2.
• Enhanced the total production of the plant.
We reply within 24 hours
+91 9767193900
Office No 207, R-cube, S.No. 116/5/1, Rahul Nagar, Warje, Pune 411052
Mon-Sat, 9am until 6pm